Top 5 manufacturing trends to watch out for in 2024 and beyond
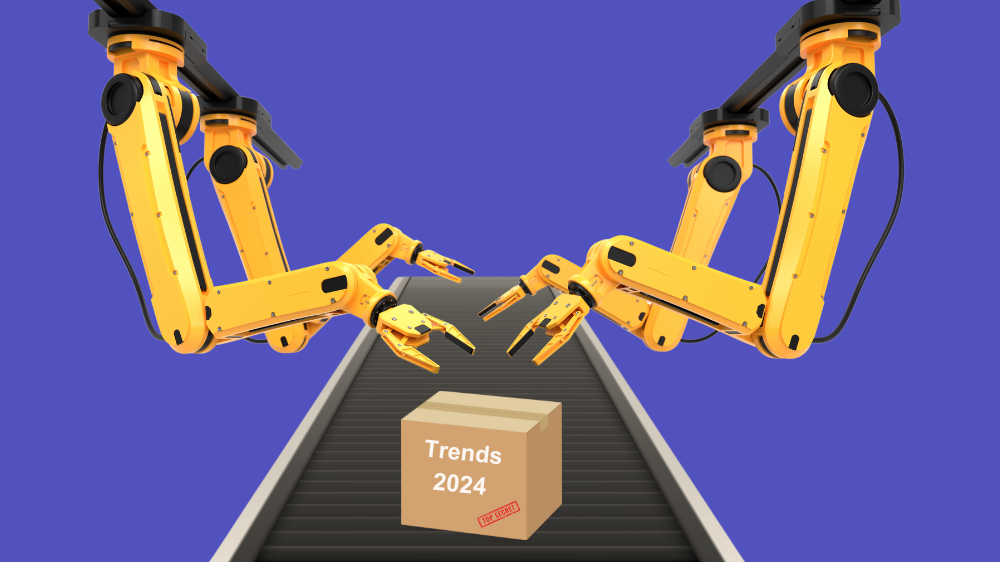
Curious to explore the cutting edge of manufacturing trends in 2024 and beyond? From Smart Manufacturing initiatives to fortified security, here’s our list.
Manufacturing is referred to as the driving force of economic growth and innovation. With a projected worldwide output of US$79.86 trillion in 2024, the manufacturing industry is undergoing profound transformations due to ever-changing consumer preferences, technological advancements, fluctuating demand and global supply chain disruptions.
Faced with this dynamic scenario, companies are at a critical juncture where the word “agility” must become a cornerstone of their operational dictionary. Navigating through challenges and seizing unique opportunities demands an unparalleled level of adaptability. As Francisco Betti, Head and Member of the executive committee World Economic Forum, observes; “The future of manufacturing is not about one company, one government, one country, it is about bringing the global community together to fix some of the global challenges that we are all facing.”
In this article, we’ll explore the top 5 trends and the fascinating developments propelling the manufacturing industry in 2024 and beyond.
#1 Smart Manufacturing initiatives as the new industry standard
Industry 4.0, commonly known as the Fourth Industrial Revolution, is the current era marked by integrating digital technologies like automation, robotics, artificial intelligence (AI) and advanced analytics into manufacturing processes. This transformation was, surprisingly, initiated around the mid-2010s and has shown unwavering momentum ever since.
Proactive manufacturers are investing in “smart factory” initiatives, integrating advanced data analysis capabilities to optimize planning, expedite design cycles and achieve enhanced visibility into supply chain and manufacturing processes. According to a recent study by Delloite, a staggering 86% of surveyed manufacturing executives believe that smart factory solutions will be the primary drivers of competitiveness in the next five years. Another survey highlights that manufacturers are quite optimistic about the industrial metaverse, anticipating a potential 12% boost in labor productivity, which could be a crucial factor in addressing the current labor shortages.
In this digital transformation, as remarkable as these advances may seem, companies mustn’t overlook one key element: involving employees in the technology design process. The aim is to ensure that technology is implemented where it has a significant impact, increasing resilience, mitigating risks and reducing costs. By actively listening to their ideas about obstacles, challenges and pain points, companies can tailor technological solutions to address these issues effectively.
#2 Keeping up with the customers‘ increasingly dynamic needs
Setting up manufacturers for success is a daunting and complex challenge, as factors such as the pandemic, changing behaviors, and new technology have further raised customer expectations. Only 57% of manufacturing salespeople feel confident in their company’s ability to adapt quickly to market changes, according to a Salesforce study.
To thrive in this dynamic environment where business agility is paramount, companies must transcend the conventional perception of customers as mere “buyers.” Instead, they must proactively engage with them, promoting an open line of communication through close sources such as sales representatives and service technicians. And yet, 51% of customers express disappointment with the way brands address their needs, and a mere 10% believe that brands truly comprehend and effectively respond to their requirements.
There is little doubt that considerable progress has been made to date. Yet, much more remains to be done to win hearts and wallets. By gaining a clear understanding of anticipated demand, manufacturers can meticulously plan production schedules, labor needs and raw material procurement, minimizing waste and demonstrating a commitment to customers’ best interests.
#3 Sustainability leading the charge in future Manufacturing development
The development of manufactured products through economically viable processes that mitigate negative environmental impacts and preserve energy and natural resources will be on the 2024 corporate agenda. Like several other movements that have gained momentum, the demand for sustainable manufacturing is expected to increase, as regulatory mandates are becoming stricter and more complex, but also because consumers are urging increasingly sustainable supply chain processes.
According to a recent Fictiv study, 87% of enterprises acknowledge the increasing significance of sustainable manufacturing, and around 55% identified improving manufacturing operations and the supply chain as a top priority.
Adopting renewable energy sources, reducing carbon emissions, applying predictive maintenance and implementing eco-friendly production methods are crucial steps in minimizing the industry’s ecological footprint while lowering costs in the long-term energy. Furthermore, the circular economy shows itself to be a growing movement towards making companies responsible for all their life cycle emissions in a closed-loop system, effectively minimizing waste and maximizing resource efficiency.
#4 Digitally connected workforce for increased productivity and business resilience
The year 2024 marks a significant shift in the industry’s approach to workforce connectivity and collaboration, driven by the ever-evolving integration of automation and artificial intelligence into daily operations. A recent study conducted by OliverWyman highlights that digital disruptions have the potential to increase the manufacturing workforce productivity by 25%.
Companies that invest in IT training and skill-development initiatives are more likely to adapt to uncertainty, just like the COVID-19 crisis and the subsequent demand for remote work, empowering their workforce to be more confident and committed to the organization. Moreover, prioritizing training acts as a powerful magnet for attracting top-tier talent. Qualified professionals are attracted to companies that invest in the development of their employees, recognizing the importance of staying ahead in an ever-competitive job market.
At the same time, manufacturers need tools that facilitate collaboration and connectivity among workers across geographical and functional boundaries. For example, Documill, a document collaboration tool for Salesforce, was created to ensure companies can finally have smooth inter-organizational communication regarding document creation, turning the once time-consuming task of keeping everyone informed into an efficient and straightforward process.
By defining standard document templates, workflows and user roles, companies can achieve their goals faster and build strong relationships. With solutions like Documill’s Leap and Dynamo, every document creation process, no matter how intricate, can be templated and reused.
Take a look at: 💡Document automation for manufacturers: far beyond just sales docs
#5 Manufacturing companies strengthening security measures
While the interconnected world of digital manufacturing offers substantial advantages to all of us, it also introduces heightened cybersecurity risks. Recent research by Deloitte reveals a concerning trend, with over half of surveyed industrial manufacturing companies falling victim to ransomware attacks.
Alarmingly, nearly 7 out of 10 of these attacks resulted in malicious data encryption.
With a surge in cyber threats and evolving compliance regulations, fortifying security measures is imperative to safeguarding sensitive data, proprietary technologies and critical operational processes. From implementing robust firewalls and advanced encryption protocols to adopting multi-layered authentication mechanisms, manufacturers are already working hard to effectively counteract the escalating threat of cyberattacks.
Last but not least, each employee plays a role in creating a security-conscious culture. Imagine it as a chess game. A single misstep may have the potential to destroy your entire strategy, like making the mistake of playing the early queen attack.
Staying vigilant and up-to-date on prevailing cyber threats allows employees to recognize suspicious activity, proactively identify potential cyberattacks and respond quickly and effectively, thus minimizing the likelihood of succumbing to cybercrime.
To conclude…
The importance of manufacturing extends far beyond the creation of goods; It acts as the driving force behind both economic growth and innovation. As we look ahead to the coming year, the long-term impacts of COVID-19, evolving consumer preferences, technological advancements, and global supply chain disruptions will undoubtedly shape industry trends. When navigating this dynamic landscape, the essence of “agility” emerges as an imperative for success. Those who are prepared to take calculated risks and promote innovative thinking will pave the way for a prosperous future.
In the upcoming year, key strategies may include:
- Improvements to operational efficiency, cutting costs and increasing revenue by capitalizing on a smart factory approach;
- Remaining competitive and responding to market dynamics by proactively adjusting strategies to align with customers’ ever-changing demands.
- The prioritization of carbon neutrality and sustainability by actively incorporating environmentally friendly practices into production processes and supply chain management;
- Fostering a digitally connected workforce to boost productivity and strengthen business resilience, helping it navigate economic uncertainty;
- Strengthening of business resilience by reinforcing security measures in response to the growing cyber threat landscape.